ICE TM technology with ESAB pending patent explores the heat excess of the Twin SAW process to increase productivity up to 100% without raising the heat input. ICE technology offers a greater production rate without the need to invest in new welding stations and increase profits.
WHAT IS THE TECHNOLOGY ICE TM ?
An energy source, three wires
The ICE technology, which is objective and simple, is the following step in the development of the
submerged arc based on the Twin technology leader of ESAB. ICE technology uses a third wire that is electrically insulated and in parallel with the two hot wires in the same contact device. ICE technology uses the heat excess generated by the welding process to melt an additional non-powered welding electrode –the Integrated Cold Electrode.
Up to now, the Twin welding has been the SAW process of a unique energy source more productive in terms of deposition rates. ICE technology made it possible to have an increase of 50% in the deposition rates compared to the double wire welding and a 100 % compared to the simple wire welding.
An old concept, more robust now.
The submerged arc welding with an additional cold wire is not a new method to increase productivity. Nowadays, there are many different technical solutions to feed the cold wire, with different performance and application areas. Most of these solutions add the cold wire to only one hot wire in the process, in a lateral angle. These solutions meet many challenges, being the stability of the process the greatest of them.
Experience has showed that these conventional solutions are not strong enough for most of the applications, since they are very sensitive to changes in welding conditions. Technology ICE TM of ESAB is designed to solve these issues and deliver a safe process insensitive to variations in welding conditions.
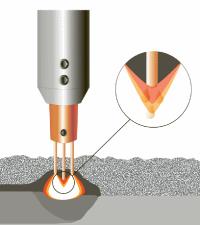
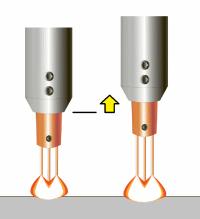
Just like Twin process (double wire)
ICE TM process uses and follows the same principle as the Twin Submerged Arc Welding, making it safe and easy to use. Penetration, the width of the weld bead, the amount of parent material melted, the mixture with the original material and the distribution of the filler metal in the weld
remain unchanged in double wire welding. Adjusting the feed rate of the cold wire, however, offers new ways of controlling the deposition rate and the reinforcement height of the weld bead.(Flat Cap Control TM).
Heat input with ICE process does not change when the same active parameters are used. The cold wire is not an active parameter, and therefore, it is not included in the heat input calculation. ESAB has carried out an investigation about cold wire for over a decade and it has showed that the cooling time between 800ºC and 500ºC remains unaltered at different amounts of wire.
Process stability
Stability and robustness are added to the process if the cold wire is integrated in the same contact device and placed in parallel with the hot wires. The additional cold wire using ICE regulation technology calms the arcs and melting. ICE technology makes the process more robust and less sensitive to changes in the arcs and adherence because the melting point of the cold wire always adapts to both arcs. The increase of the process stability makes it easier to adjust and adapt the different joint types.
The exclusive method of ESAB process regulation, in combination with the PEK process controller, friendly user, makes ICE TM technology easy and safe. Only one parameter has to be set and the ESAB controller does the rest. The new process regulation method controls the feed speed of the cold wire independently of the hot wires. This improves the process stability and adapts the welding process automatically to the changes in the welding conditions, ensuring a safer and more productive process.
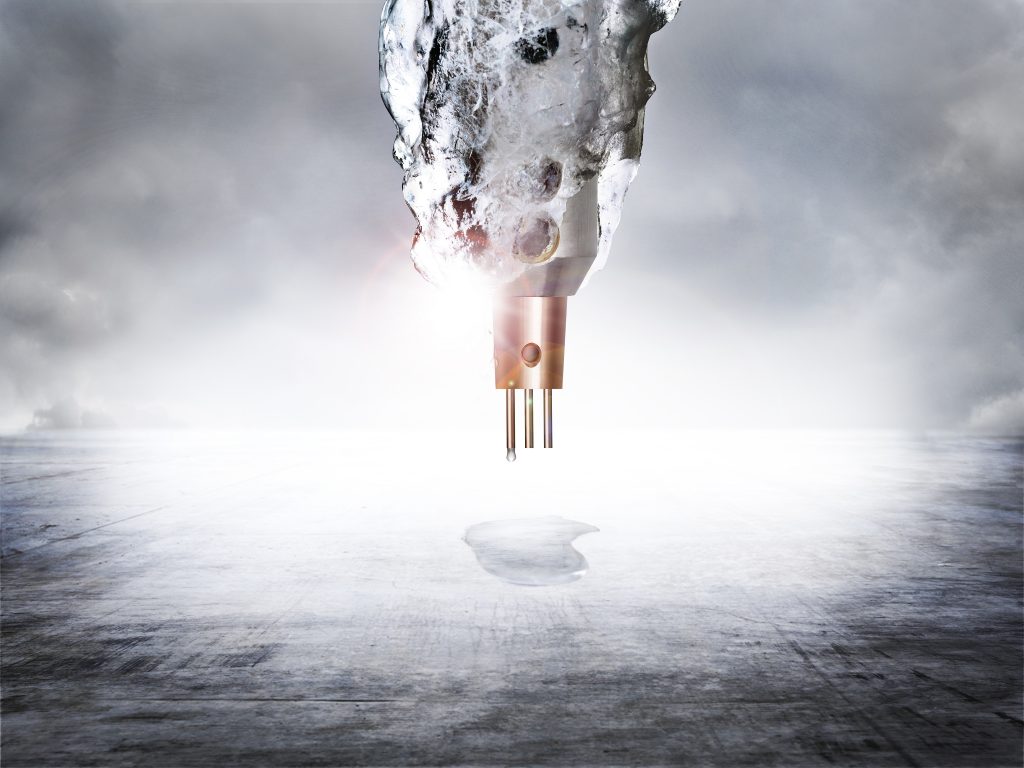
ESAB Argentina- Conarco/ Murature 4079 (B1672AWG) Villa Lynch- San Mari